Taking float glass as an example, the three major thermal equipment in glass production include float glass melting furnace, float glass tin bath and glass annealing furnace. The development of glass production technology depends to a large extent on the improvement of refractory brick manufacturing technology. Therefore, the reasonable selection and use of refractory bricks is very important in the design of glass melting furnace.
Refractory Bricks for Various Parts of Glass Kiln
Parts in Contact with Glass Liquid
The melting part and cooling part of the pool wall are the parts in direct contact with the glass liquid. They are extremely susceptible to high temperature, chemical erosion caused by glass liquid and mechanical and physical erosion caused by flow. Therefore, the refractory bricks used in this part must have good resistance to glass liquid erosion. At the same time, it cannot pollute the glass liquid.
Domestic glass kilns are generally built with fused zirconium corundum bricks. AZS refractory bricks have excellent high temperature and glass liquid resistance. This is because it contains a eutectic of baddeleyite zircon and α-Al2O3 with very good corrosion resistance. Therefore, it is very suitable as a pool wall brick for the melting part of a glass kiln.
Parts not in Direct Contact with Glass Liquid
The tank kiln is a complex and large masonry built of various refractory materials. Its vaults are mostly made of silica bricks. The regenerator of the glass kiln uses sintered mullite bricks and high-alumina bricks. Moreover, the silica bricks produced by Kerui Group do not pollute the glass liquid. In other words, Kerui factory can provide cost-effective refractory bricks for different glass kiln equipment.
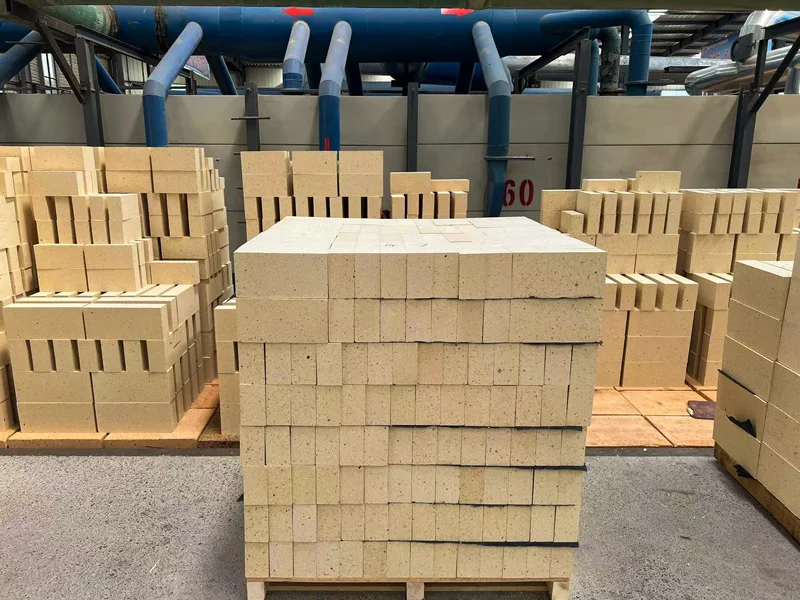
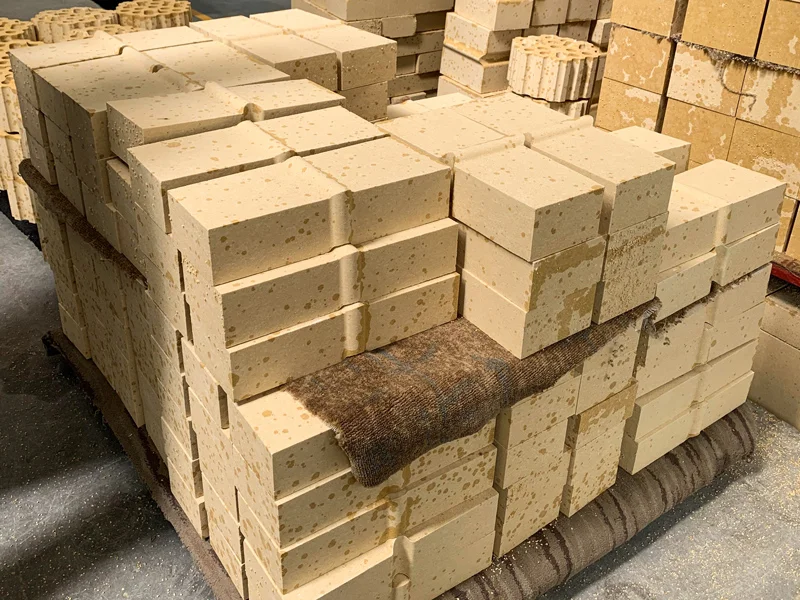
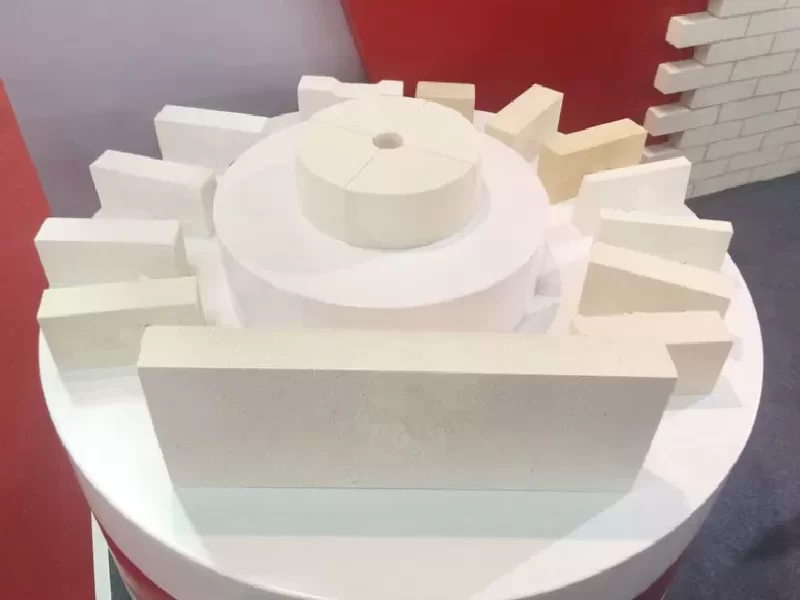
Besides, if you are not sure what refractory materials you need for your glass kiln, please contact us. Kerui’s technical engineers will provide you with detailed solutions. Contact us now for free technical support and quotes.