The cement rotary kiln operates in a harsh working environment such as high temperature, chemical corrosion and physical wear. It requires the use of a variety of refractory materials to protect the kiln body and extend its service life. In addition, the working environment of each part of the cement rotary kiln is different. Therefore, the refractory materials they need are also different.
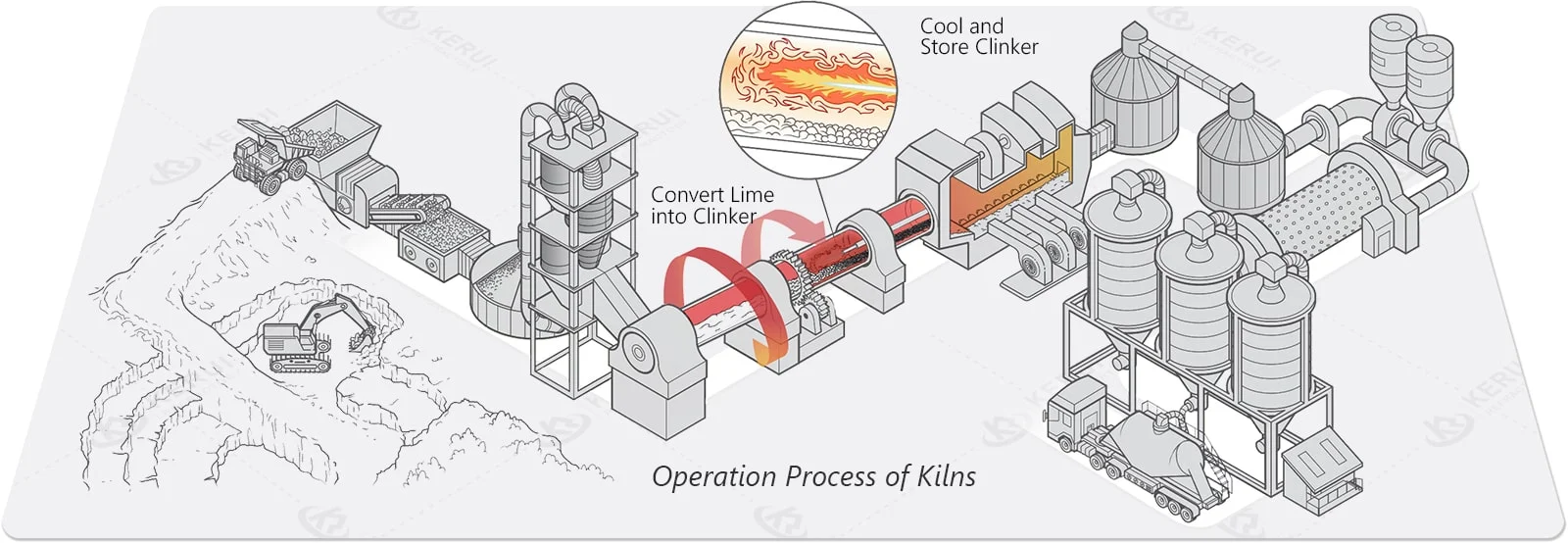
Refractories for Various Parts of Cement Rotary Kiln
Preheater
Currently, the refractory materials commonly used in preheaters are mainly alkali-resistant castables and alkali-resistant bricks. They can resist the erosion of alkaline materials on preheaters.
Decomposition Furnace
The working conditions of the decomposition furnace are relatively harsh. Therefore, there are specific requirements for the selection of refractory materials. Usually we choose anti-stripping high alumina bricks, alkali-resistant bricks and alkali-resistant castables.
Tertiary Air Duct
The tertiary air duct needs to withstand high temperature, high-speed airflow and wear of clinker particles. Therefore, we use alkali-resistant bricks and alkali-resistant castables to resist high-temperature erosion.
Rotary Kiln
- Front and rear kiln mouths: the front and rear kiln mouths of cement rotary kiln are the weak links of kiln lining. They need to withstand the impact of rapid cooling and rapid heating air flow, the wear of high temperature clinker, and the alkali corrosion of high temperature harmful gas. Therefore, we usually use steel fiber reinforced refractory castables.
- Upper and lower transition zones: the temperature fluctuations in these areas are large, and the kiln skin is not easy to stabilize. Commonly used refractory bricks are magnesia alumina spinel brick, aluminum silicon carbide brick, anti-stripping high-alumina brick, magnesia-alumina-chrome brick and phosphate-bonded high alumina brick.
- Firing zone: the firing zone of cement rotary kiln is directly related to the quality and output of cement clinker. Its working temperature is usually 1300℃(2372℉)-1450℃(2642℉). Commonly used refractory bricks are directly bonded magnesia-chrome bricks, magnesia-iron spinel bricks, dolomite bricks and magnesia-calcium bricks.
Kiln Door Cover
Its function is to protect the kiln head from high temperature and chemical corrosion. At the same time, it also prevents heat loss and leakage of harmful gases. We use anti-stripping high-alumina bricks or 75% high-alumina bricks for masonry.
Cooler
The cooler of cement rotary kiln is mainly used for rapid cooling, transportation and heat recovery of high temperature clinker. The selection of refractory bricks is mainly anti-stripping high-alumina bricks and phosphate-bonded high-alumina wear-resistant bricks.
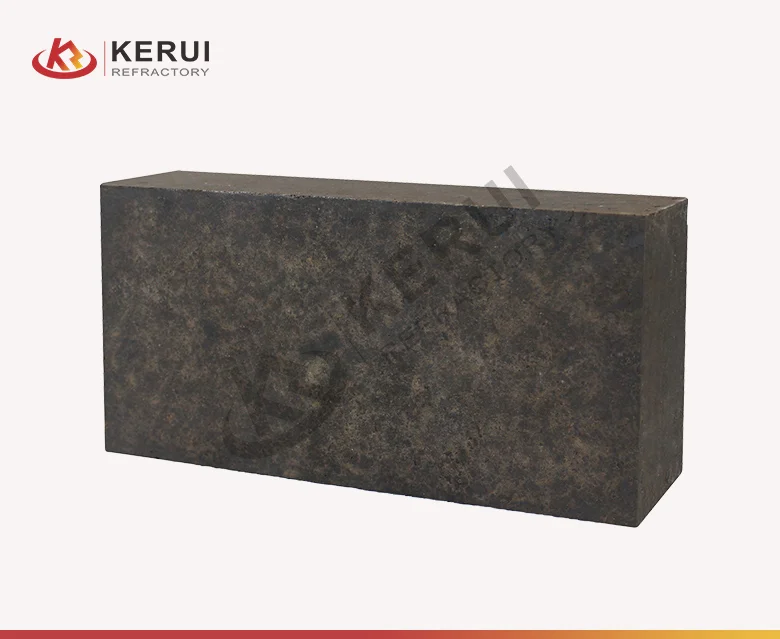
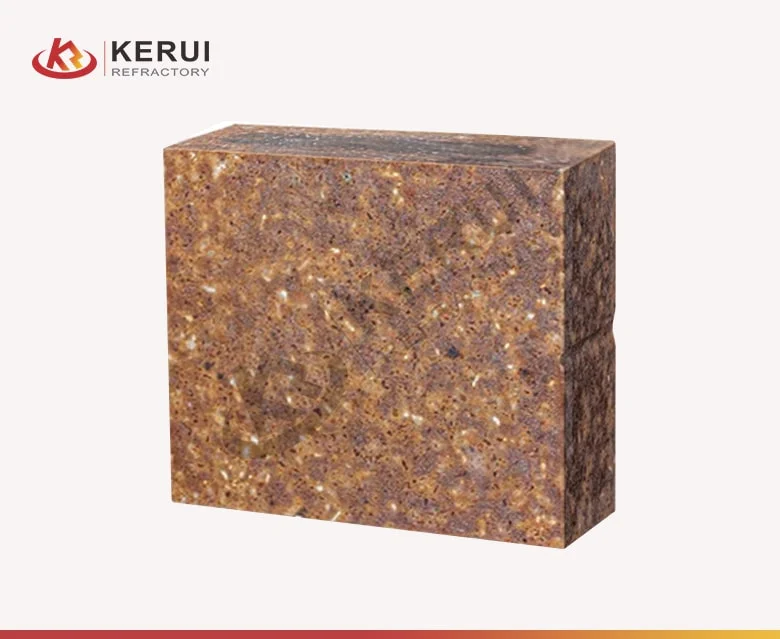
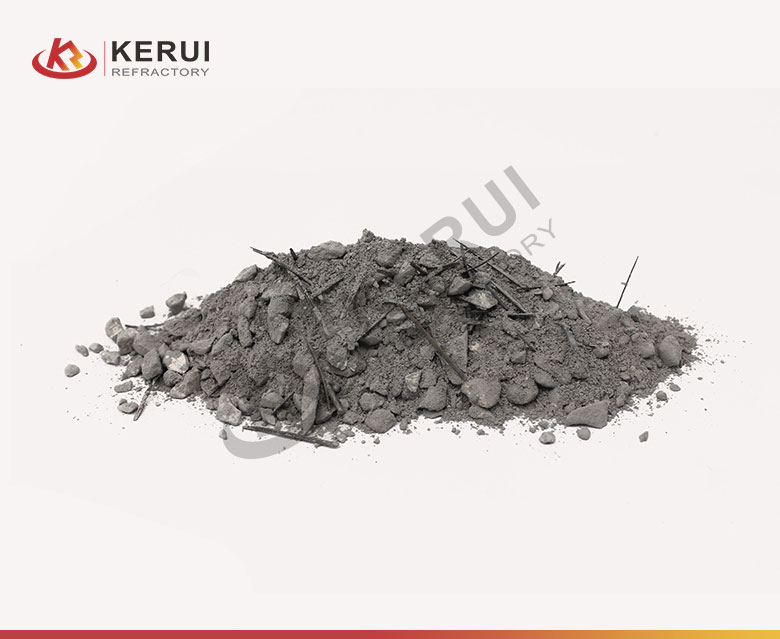
Using the right high-quality refractory materials for each part of the cement rotary kiln can greatly extend its life. If you still don’t know what refractory bricks to choose for your rotary kiln, please feel free to consult KERUI. Kerui Group China provides you with a one-stop refractory solution for kilns!