Fire clay brick refers to refractory brick with an Al2O3 content of around 30-45%. According to statistics, its usage accounts for an astonishing 60% in the refractory industry! Because it is the most cost-effective and widely used refractory brick. As an experienced clay brick factory, Kerui has become a long-term partner of internationally renowned companies, including RUSAL, CHALCO, ALBA, POSCO, PSM, etc.
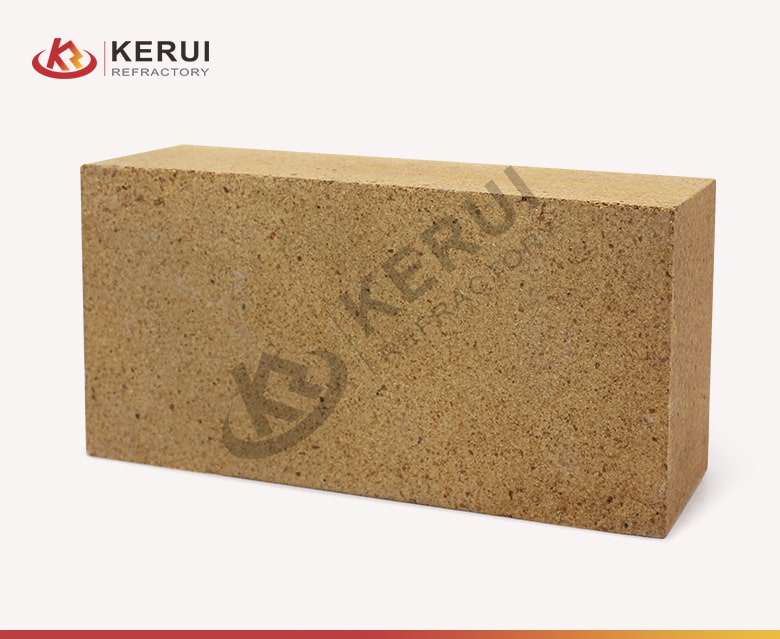
Technical Data Sheet of Fire Clay Brick
According to the international refractory industry standards, refractory clay bricks are divided into SK series according to the Al2O3 content. Usually there is sufficient stock and fast delivery in Kerui factory. The following data sheet is the technical parameters of standard clay bricks. It is worth noting that Kerui supports customization according to drawings or kiln operation conditions.
Note: There are also N series clay bricks according to China Metallurgical Industry Standards. Contact Kerui for more technical details.
Item/Grade | SK-30 | SK-32 | SK-34 | SK-35 | |
---|---|---|---|---|---|
Al2O3, % | ≥ | 30 | 35 | 38 | 45 |
Fe2O3, % | ≤ | 2.5 | 2.5 | 2 | 2 |
Refractoriness (SK) | ≥ | 30 | 32 | 34 | 35 |
Refractoriness underload, 0.2MPa, °C | ≥ | 1250 | 1300 | 1360 | 1420 |
Apparent Porosity, % | ≤ | 22-26 | 20-24 | 20-22 | 18-20 |
Bulk Density, g/cm³ | ≥ | 1.9-2.0 | 1.95-2.1 | 2.1-2.2 | 2.15-2.22 |
Cold Crushing Strength, MPa | ≥ | 40 | 45 | 30 | 40 |
Fire Clay Bricks Price from Kerui Factory
The fire clay bricks price starts from 50$ per ton. (GURANTEE FACTORY PRICE!!!)
If customers compared the same quality on the high temp refractory bricks market, you’ll find that Kerui is providing a sincere price. Because we can reduce cost of the third party.
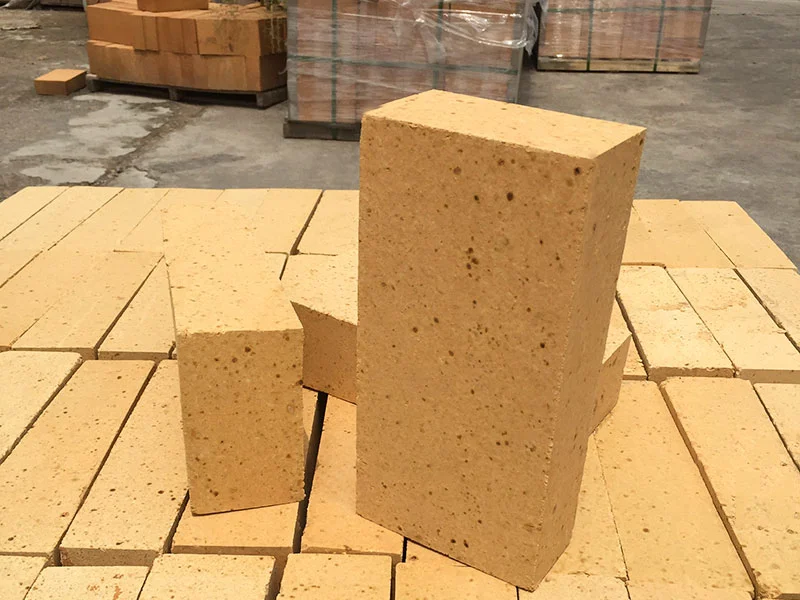
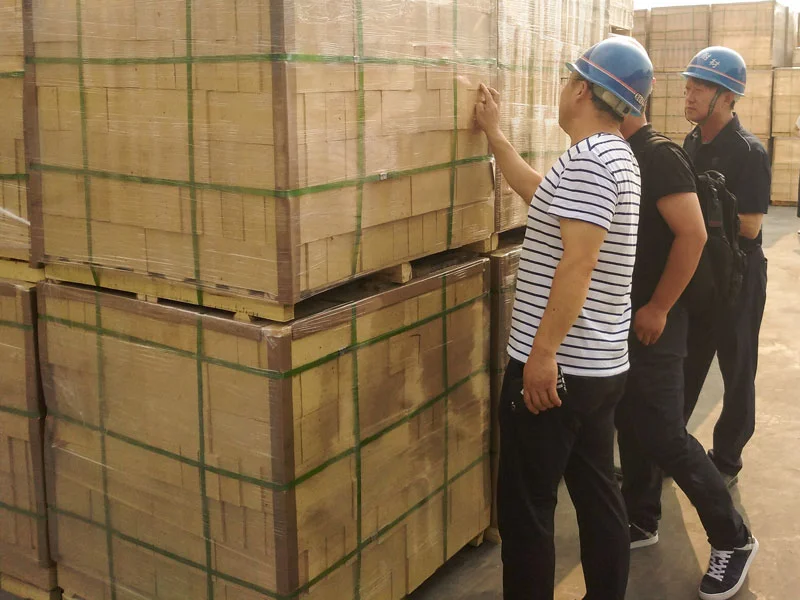
Package and Delivery of Kerui Fireclay Bricks
Package: pack in boxes (optional), pallets and container;
Delivery: immediate shipment for standard fire clay brick, 7-15 working days for customized fire clay bricks.
Application of Kerui Clay Refractory Brick
The clay fire bricks for sale belong to acidic refractory bricks. The fire clay bricks uses to acidic corrosion increases with the increase of SiO2 content. Therefore, Kerui clay refractory bricks are particularly suitable for the lining of acid kilns. Common applications include the linings, doors and other areas about:
- Blast furnaces;
- Waste incinerators;
- Glass furnaces;
- Carbon baking furnaces;
- Boilers;
- Rotary kilns;
- Ceramic kilns;
- Coke oven;
- etc.
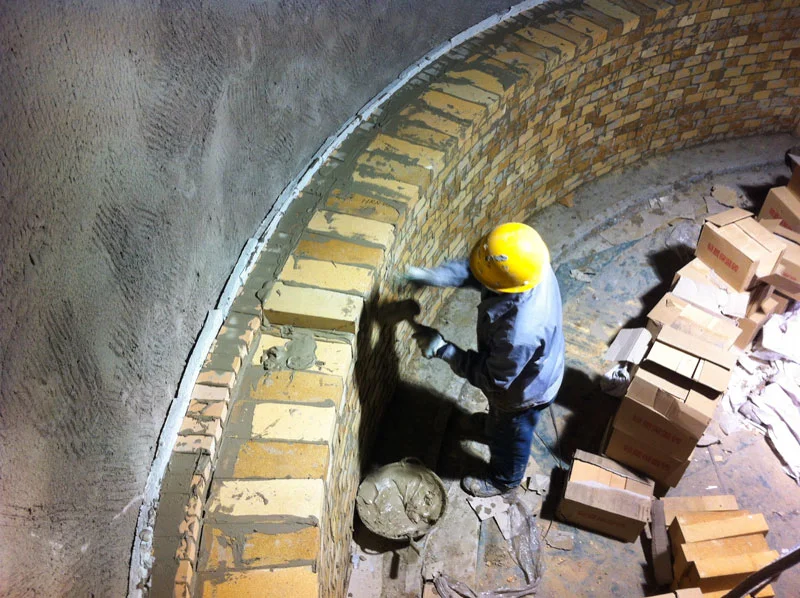
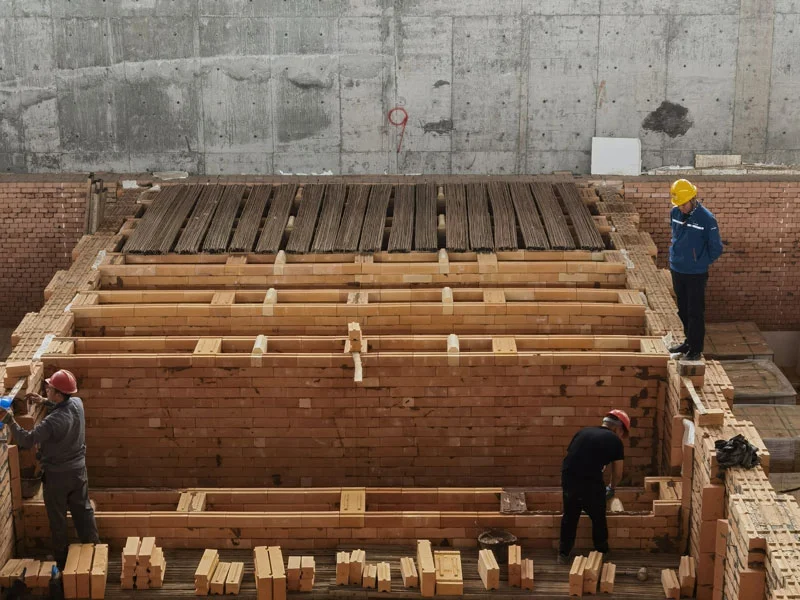
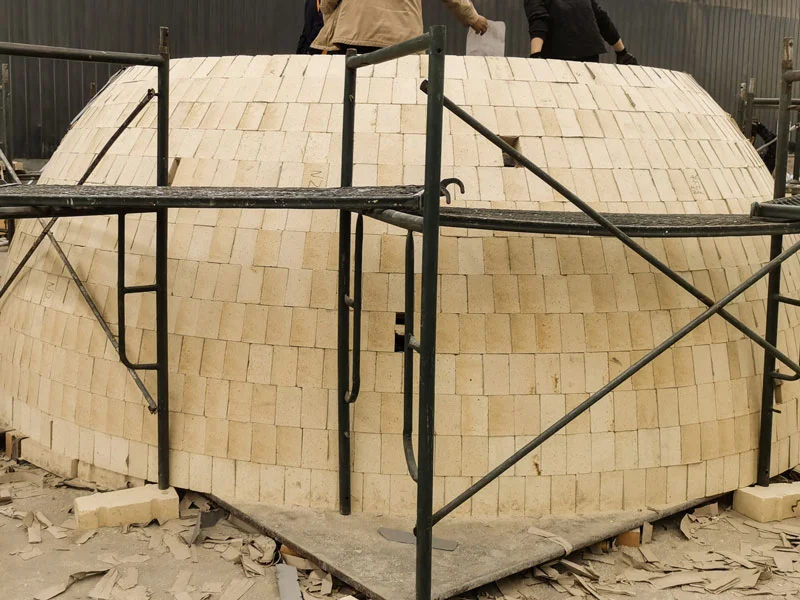
Get a Professional Fire Clay Brick Solution from Kerui
It’s wise to tell Kerui the kiln you operate when inquiring. In this way, you can get a more accurate and professional clay brick solution. For example, refractory bricks for blast furnaces require higher strength and wear resistance. Besides, clay fire bricks for hot blast furnaces require better creep resistance, thermal vibration stability, etc. Moreover, fire clay blocks for glass kilns require larger sizes and higher SiO2 content, etc.
If you’d like to catch Kerui latest cases, please follow Kerui Pinterest.
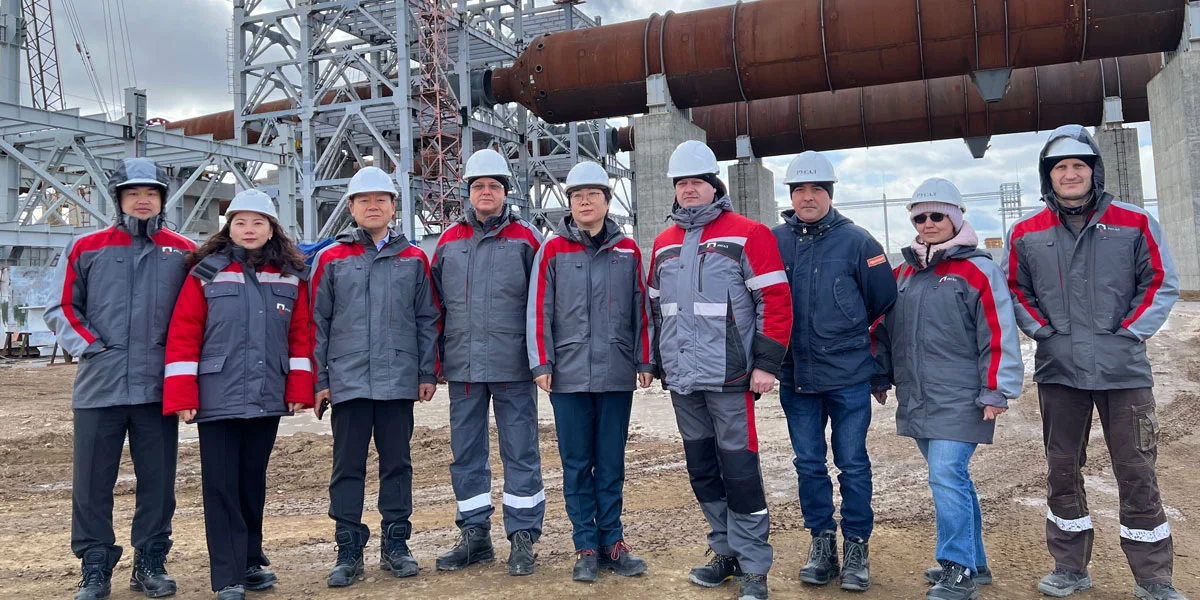
Benefits of Using Fire Clay Refractory Brick
- Good Acid Corrosion Resistance
- High Working Temperature
- Good Thermal Shock Resistance
- Good Anti-peeling Property
- Good Volume Stability
Reduce Cost
Commonly, fire clay refractory products are used for large-area paving of high-temperature industrial kilns. In order to achieve stable operation of the kiln, customers can choose to use high-end refractory bricks in specific areas (furnace roof, furnace door, furnace seam). This is the most cost-effective kiln construction solution.
Short Construction Period
As the most commonly used refractory material, fireclay bricks and the ingredient like clay refractory mortar usually have sufficient stock. Therefore, choosing fire clay bricks for sale as kiln lining can achieve fast delivery and advance the construction period. In addition, Kerui supports customized clay brick sizes to facilitate customers to complete large-area kiln construction in a short time.
Long Service Life
Kerui strictly controls the quality of clay refractory bricks. Therefore, even if this product is low-priced, it can achieve a long service life if you use it in the right environment. Kerui will also provide technical support to extend he service life of your kiln.
Fire Clay Bricks Manufacturing Process
-
- Mixing: After strict inspection by the quality inspection department, the raw materials of clay clinker and other additives are uniformly mixed by Kerui fully automatic batching machine and mixing system.
- Forming: With 20 units of 60 ton press machines, we efficiently and precisely produce the clay bricks you need.
- Drying: The refractory fire clay bricks automatically enter the drying kiln to evaporate excess moisture, preventing subsequent cracking and deformation.
- Sintering: Kerui Refractory has introduced two 168-meter-long high-temperature tunnel kilns, where the internal substances of the clay bricks undergo transformation to form a strong structure.
- Cooling: The clay bricks release internal stress through natural cooling.
- Packing: After passing secondary quality inspection, the finished clay bricks are packed. Kerui uses high-quality plastic film, steel bands, and sterilized pallets for strict packaging to ensure safe delivery to customers.
- Shipping: Kerui shipping department collaborates with internationally renowned logistics companies to provide customers with the most cost-effective shipping solutions. We fulfill delivery according to the contract.
Fire Clay Bricks Manufacturer – Kerui Refractory
Advanced equipment: PLC control system, fully automatic batching system, 60 ton press machines;
Superior quality: high purity raw materials, strict quality inspection system, physical and chemical laboratory;
Efficient supply: fast production, quick shipment, sufficient stock;
Reliable after-sales service: experienced technical engineers, regular return visit,
…