High-alumina refractories are highly suitable for hot blast furnaces, especially in areas with severe abrasion, such as the furnace bottom. Additionally, it is worth noting that regardless of whether it is high-alumina bricks or other products, such as high-alumina castables, the aluminum content must be at least 70%—75% or above to ensure better usage effects.
High Alumina Refractory Bricks for Hot Blast Furnaces
In the refractory industry standards, high alumina bricks such as LZ-75 and SK-38 have an aluminum content of over 75%. Compared with products of other grades, the thermal shock stability and slag resistance of this product are enhanced.
Advantages
- Excellent performance: High alumina bricks undergo high-pressure molding and high-temperature sintering, resulting in high density and the ability to resist rapid temperature changes.
- Convenient construction: Can be constructed using conventional masonry methods.
Disadvantages
- Long construction period: Due to the processes mentioned earlier, refractory bricks must have a production cycle of 7 to 10 days. In some cases where the sintering task is urgent, it may take more than 20 days.
- Brick joints are weak areas: When masonry is carried out, high alumina refractory mortar needs to be used in combination. Brick joints are weak areas.
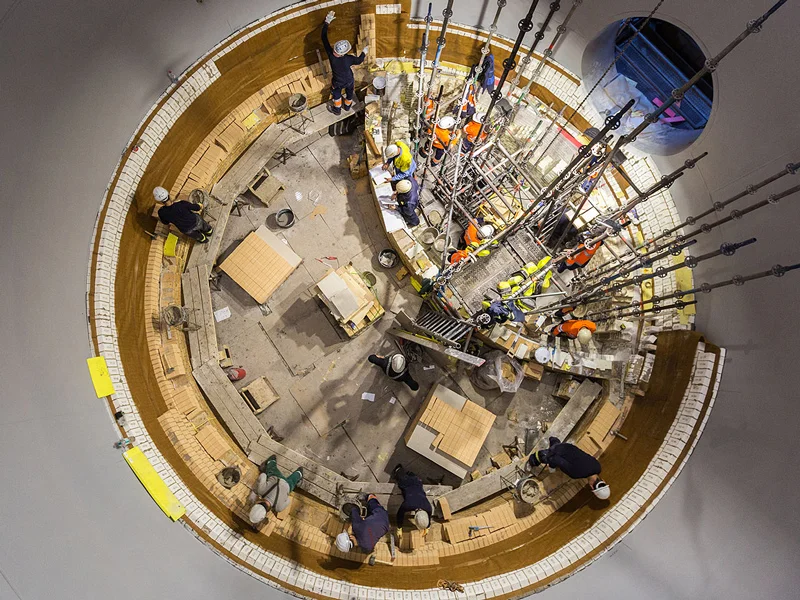
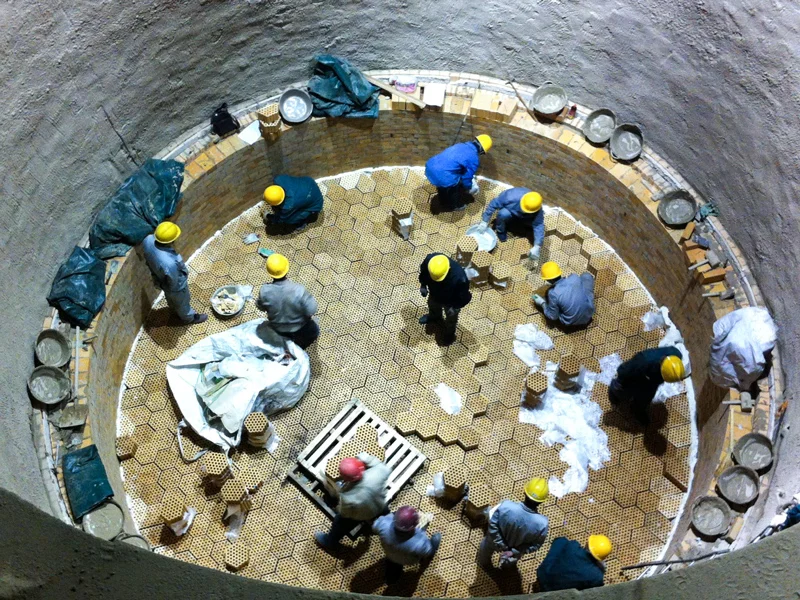
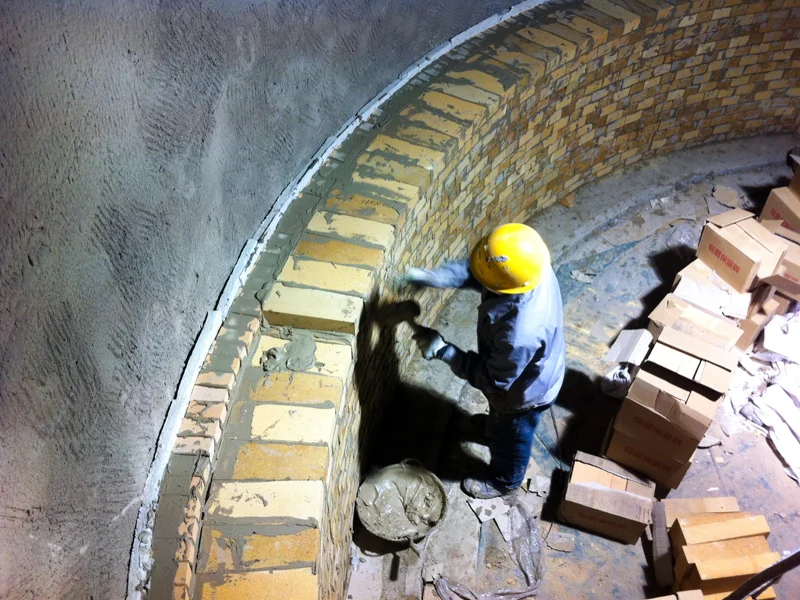
High Alumina Monolithic Products for Hot Blast Furnaces
To achieve good sealing performance and excellent performance in irregular parts of hot blast stoves, some customers may choose low-cement castables with an aluminum content of 70% – 75%. The advantage of castables is that they are cast integrally, convenient for construction, and have good air tightness.
Advantages
- Good air tightness: Integral casting construction without brick joint connections.
- Fast production cycle: Generally, the production of castables can be completed in 2 – 3 days. In some urgent cases, finished products can be produced on the same day. If the construction period is tight, refractory castables can be selected.
Disadvantages
- Poor thermal shock resistance: Refractory castables have not undergone high-temperature treatment. Their slag resistance and thermal shock resistance are inferior to those of high alumina bricks and are only suitable for areas with less severe erosion.
- High construction requirements: The construction of high alumina castable requires strict control of the mix ratio, mixing, pouring and curing. Otherwise, quality problems are likely to occur.
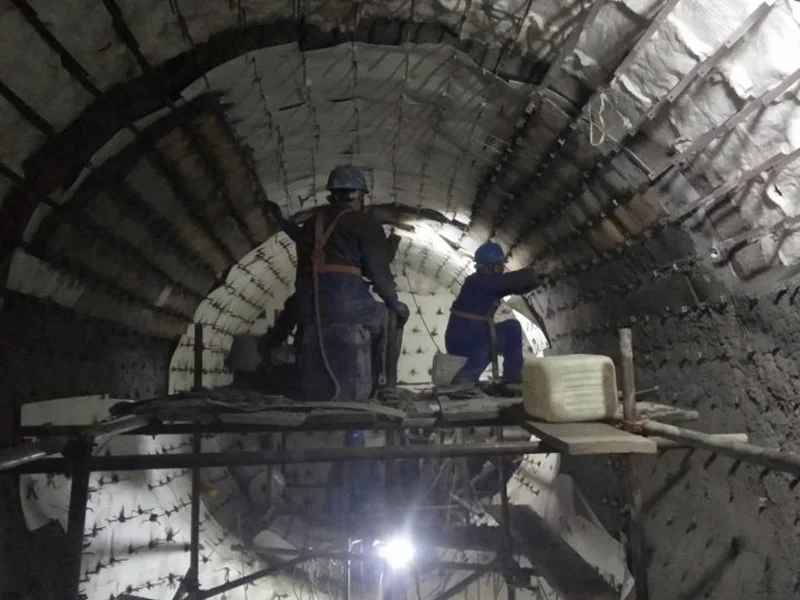
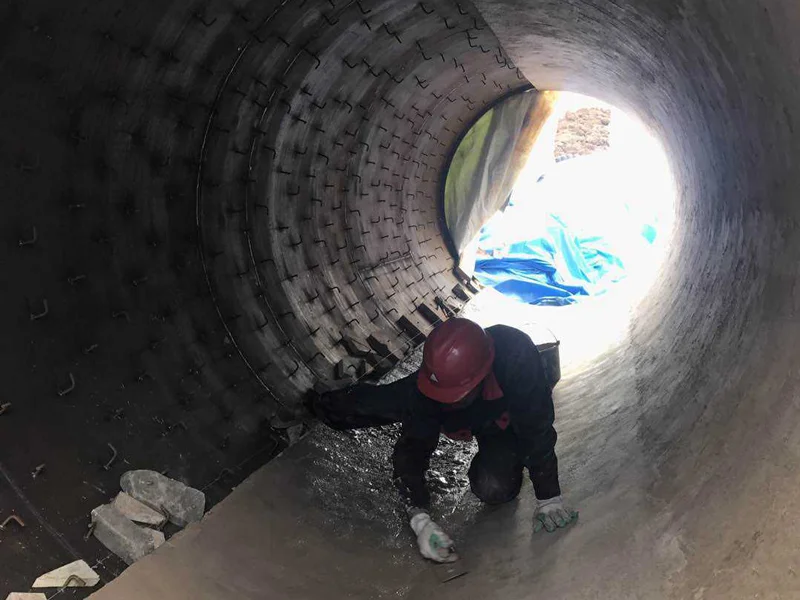
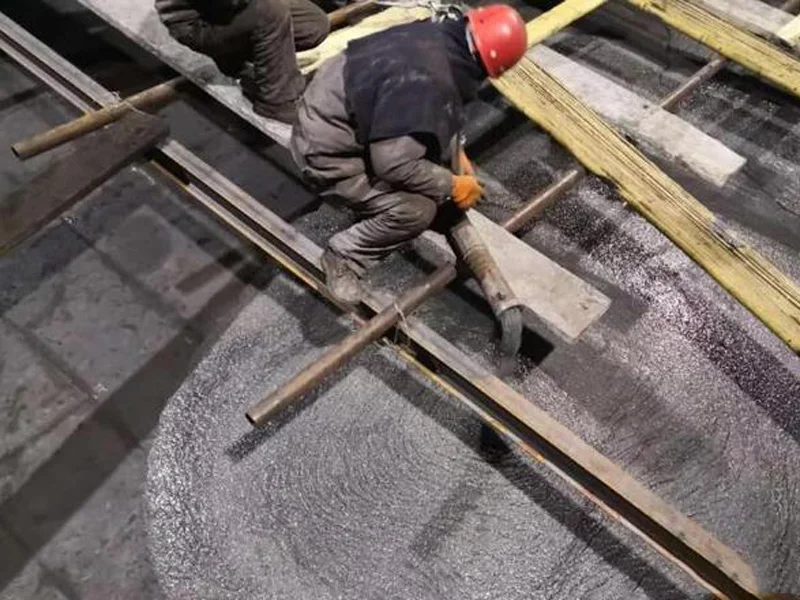
In conclusion, high alumina refractories are crucial for hot blast furnaces. No matter which product you decide, quality to meet usage requirements is an important link. If you’re still puzzled about the option for refractory material for a hot blast furnace, Kerui is glad to provide a professional solution!